Pure aluminum and aluminum/alumina blend powder coatings are shown. Although it breaks down relatively easily, it is silica free with minimal iron content (2%) and produces a luster-white metal finish. Best used for: Any abrasive blasting that requires minimal debris creepage out into the environment. Centrifugal blasting is also known as wheel blasting. They concluded, Thermodynamics indicate that if only secondary forces are acting across the interface, water will virtually always desorb an organic adhesive from a metal oxide surface. This suggests that simply cleaning the adherend surface is not an adequate treatment for structural bonding applications. very effective at removing certain contaminants from the surface of materials, Everything You Need to Know about Industrial Metal Finishing. It should not be used on stainless steel where iron impregnation is a concern. Blasting of baking soda is unique because of its biodegradable characteristics. If absolutely necessary, bonding can be carried out after periods of time up to 14 days SET with only moderate strength loss. When a coating is applied to such a surface the valleys are filled in with coating.
16.5. Effect of surface roughness on the interlaminar peel and shear strength of the CFRP/Mg laminates. Occasionally, the abrasive is propelled by pressurized water. Shot blasting is used primarily to rid metals of corrosion and rust, while shot peening is the preferred method to toughen metal and increase its strength. Our process ensures increased fatigue strength, prevention of cracking and fretting, reduction in brittleness, and the ability to curve or strengthen parts without creating tensile stress. Because of the fine-sized nozzle, pressure can also be adjusted with these machines to do a lot more than surface cleaning. The coating thickness is an indication of the deposition efficiency of the process, since the powder feed rate was equal for all runs. This modification differs based on the type of abrasive used. blasting grit forcibly abrasive A machined bottom of a fry pan. This shock helps to break any bonds between the surface and the contaminant helping to dislodge it. It can be programmed to even cut, drill, or deburr surfaces. Small amounts of parent material may be removed in this process. Heat from the spraying process has minimal impact on the coated part temperature. Software updates, Resources The alumina particles appear black in a white aluminum matrix for the case of the aluminum/alumina blend.
The quality and reliability of the coatings depends on careful control of coating material source and spraying parameters. This type of treatment is applied more for abrasion or scratch resistance than for adhesion. HELFRITCH, in The Cold Spray Materials Deposition Process, 2007. The inert gas carries the molten metal droplets to the substrate. The abrasive shatters on impact with the surface and exerts a force that clears up contaminants on the surface. It is angular in shape. This process forms small indentations in the surface with enough force to sufficiently strengthen the metal and relieve stress. Processes, Applications Plastic grit is another soft medium, typically in a size range of 1260 mesh. Grit blasting is the most widely used surface texturing method since it provides a rough surface with low effort and can be easily implemented in industrial applications. Grit blast profiles are commonly measured in microinches or root mean square by means of a profilometer (see Section 5.3). Intermediate cleaning is the process of removing soil from a surface by physical, mechanical, or chemical means without altering the material chemically. Finally, the near-white grit-blasted surface has high compressive stresses or strains and a beneficial absence of mill scale. They concluded that the best results were obtained when the grit size was matched to the size of the filler material in the adhesive.
Full coverage of the grit blast is indicated by lack of gloss on the metal surface when viewed at a flat grazing angle. This leaves the surface smooth and uniform. The one verified case of high pH SCC on a thin-film fusion bond epoxy pipeline occurred at a rock dent where the coating was damaged; the rock provided the shielding necessary for cracking. Shot peening is often confused with shot blasting, but these two processes have very different effects. Glass Cuts - The thing about glass cuts are that they are present in different variations from course to highly refined media but the work of both is excellent in giving the surface a new lustrous and reflective look. However, when this procedure is used for a dissimilar metal substrates such as aluminum, there is potential bimetallic corrosion. Contact| The choice of which grit to use depends on its intended purpose, the substrate, and the expense. Grit blasting is a technique that creating surface textures by the impact of hard particles.
Each has its own properties, which makes each one ideal for varying situations. Full coverage of the grit blast is indicated by lack of gloss on the metal surface when viewed at a flat grazing angle. Grit blasting is a relatively simple process. We believe that shot peening is the best option to treat critical parts used in industrial environments.
The sharpness of the abrasive and the consistency in size made it a great abrasive to use in giving uniform finished.
They measure neither uniformity or coverage of the grit nor the sharpness of the peaks. Finally, bead blasting is another air pressure powered abrasive blasting method that uses glass beads. Laurence W. McKeen, in Fluorinated Coatings and Finishes Handbook (Second Edition), 2016. Grit blasting The biggest benefit to this method is that it doesnt use compressed air pressure making it much more.
There are numerous types of grit. Grit blasting (or sand blasting) is a type of protective treatment that attempts to smooth out a part. They concluded that some improvements they observed in durability were strictly related to the increased surface area of the grit-blasted surfaces. Shot peening It is thus a plot of conductivity versus depth into the coating. Denser materials have more momentum and impart more energy to the substrate. It is often made into waterborne slurry and propelled by high-pressure water. The use of steel grit also has added advantages such as providing smoother surface finish and helping in peening which strengthens the metal. There are three main parts to any abrasive blasting tool regardless of what the specific material does to surface. Table 16.3. For reinforcement of a substrate or creating a very rough surface, a discontinuous layer of stainless steel such as 309 alloy may be applied to grit-blasted metal. Zinc conductivity as a function of depth over an aluminum substrate. This involves a blasting machine that comes equipped with a vacuum suction that removes any propelled abrasives and surface contaminants. Shot peening is a mechanical process that helps improve surface residual stresses for industrial metal parts. Everything You Need to Know About Powder Coating. Arc spray is most common. The rinse sometimes creates an oxidizing or rusting problem. Videos Waterjet cleaning The abrasive is soft, friable dried shells or nuts. Blasting with glass bead will produce a metallurgically clean surface for parts and equipment. Chemical etching using acidic materials, such as phosphoric acid, chromic acid, hydrochloric acid, or sulfuric acid or bases such as sodium hydroxide, gives smooth peaks, without the sharp tooth required for best adhesive bond. Its a unique form of abrasive blasting as the carbon dioxide is non-toxic and doesnt react with the contaminant on the part surface making it ideal for substances such as cleaning food processing equipment. Let's first clear up your mind about what is the Grit Blasting is and how does it function.
Solvent cleaning should always be carried out before this step. Whats universally true though is that its a much more effective way of cleaning surfaces and is more cost-efficient. Parts can also be pre-heated up to 200C to improve coating adhesion. Excessive noise and light radiation requires personal protective equipment. A drawback however to soda blasting is the abrasive cannot be recycled. Medical They found that increase particle size from 120150m to 380830m produced rougher surfaces. This process is used for cleaning or for preparing the surface for welding and also for adhesion of the coating. You must have heard about Grit blasting and its effects? Is Abrasive Blasting the Right Finish for You? This abrasive material is also fairly cheap to acquire and most abrasive blasting machines have been proven to be far more effective than other methods in terms of efficacy that is better and faster cleaning of surfaces. Significant differences in adhesion and conductivity can be seen. A profilometer drags a diamond stylus across the substrate and measures the depth of the peaks and valleys (Table 5.3). A finish machining process is usually required, e.g. As a result, this method is no longer preferred when it comes to abrasive blasting as the abrasive can be inhaled or leak into the environment. Coating bond strengths of up to 70 MPa can be achieved, although this is low in comparison to other coating processes. FAQs Porous surfaces can be sealed using wax (for low service temperatures), silicone and epoxy resins (for higher temperature/high humidity service environments). document.getElementById( "ak_js_1" ).setAttribute( "value", ( new Date() ).getTime() ); The periodic table is narrowing by the day, and scientists have fewer options for finding a compound with great coating qualities. Automotive Machine sanding has given slightly better results than hand sanding. Copyright 2022 Elsevier B.V. or its licensors or contributors. Glass-reinforced plastic laminates prepared for bonding by hand- and machine-sanding can be stored to 30 days at 23C and 50% RH with no adverse effect on bond strength.
Typical applications for baking soda include graffiti removal, boat hulls, and large printing press rolls. abrasive abrasives gravity specific hardness types which particle use blasting cleaning materials Hard grit is propelled by compressed air, or occasionally by high-pressure water, at the substrate needing cleaning or roughening. Some are even used against diamonds to alter their surfaces and in applications such as glass etching. Theres no abrasive that needs to be recycled or cleaned up. The biggest advantage and use for pencil blasting are when precision is needed. The abrasive used varies based on the surface treatment required. PRIMS Pro A photo of one example is shown in Figure8.8. This figure shows the conductivity of coatings as a function of the skin depth of the applied magnetic field. K.G. Glass beads are often used for stress relief. These results demonstrate the advantage of grit blast to the quality of the coating, and all coupon substrates used in the subsequent tests were grit blasted. They all have some mechanism to blast surfaces with an abrasive material that is, to propel abrasive at the surface at incredible velocities. This could be due to the relative softness of the substrate, or because the texture of the substrate or pattern machined in the substrate needs to be maintained. Figure 6.6.
With other clean substrates, the order of these two operations is not important.
Bristle blasting is the only blasting that doesnt involve an abrasive being projected onto a surface in order to clean it. blasting blast dry suction cabinets pressure cabinet guns nozzles gun diagram abrasive machine wet air glass hopper start need This makes them suitable for softer surfaces such as chrome, plastic, or glass. Many times it is necessary for sample processing to take place to lock in the final media type and size. Plastic grit, walnut shells, or sodium bicarbonate can clean the substrate or remove the previous coating. Powder coating is a type of dry coating often used as a finish on industrial equipment as well as home goods. Baking soda is commonly used where one-pass coverage with no recovery is acceptable or desirable, and the substrate is delicate or sensitive. Search| In addition, the etching reagents require immediate rinse to stop the action and prevent salts from depositing on the surface. If you are looking for a process to clean out any surfaces of your belongings then you are in the right place. [67] found that grit blasting can enhance bonding between polyamide and AA6082 while a higher pressure did lead to a higher bonding strength (Fig. But even when chemically analyzed virgin grit material is used, tests have shown that the method yields bonds to steel adherends exhibiting poor durability. Contact us today to inquire about utilizing our shot peening service. Silicon carbide is usually offered in a size range of 16240 grit. Grit blasting, also known as Sandblasting is a mechanical process of removing dust, rust, and impurities from the surface of any material. It uses silica or quartz as the abrasive material, which is then propelled onto surfaces at high speed. of Shot Blasting Machine, Shot Blasting Machine for Surface The different media types have different hardness, shape, and density, and each is available in a wide range of particle sizes. One surprising result of the laboratory and field studies was that a light brush blasted surface was actually more susceptible to SCC than a mill scaled, wire brushed surface and that a near white surface finish was required for adequate SCC resistance [6,7].
16.5. Effect of surface roughness on the interlaminar peel and shear strength of the CFRP/Mg laminates. Occasionally, the abrasive is propelled by pressurized water. Shot blasting is used primarily to rid metals of corrosion and rust, while shot peening is the preferred method to toughen metal and increase its strength. Our process ensures increased fatigue strength, prevention of cracking and fretting, reduction in brittleness, and the ability to curve or strengthen parts without creating tensile stress. Because of the fine-sized nozzle, pressure can also be adjusted with these machines to do a lot more than surface cleaning. The coating thickness is an indication of the deposition efficiency of the process, since the powder feed rate was equal for all runs. This modification differs based on the type of abrasive used. blasting grit forcibly abrasive A machined bottom of a fry pan. This shock helps to break any bonds between the surface and the contaminant helping to dislodge it. It can be programmed to even cut, drill, or deburr surfaces. Small amounts of parent material may be removed in this process. Heat from the spraying process has minimal impact on the coated part temperature. Software updates, Resources The alumina particles appear black in a white aluminum matrix for the case of the aluminum/alumina blend.
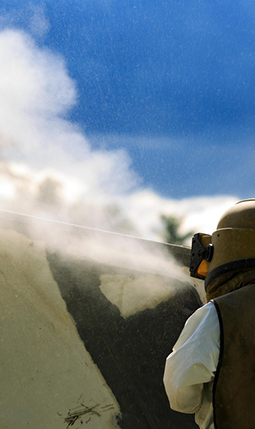
Full coverage of the grit blast is indicated by lack of gloss on the metal surface when viewed at a flat grazing angle. This leaves the surface smooth and uniform. The one verified case of high pH SCC on a thin-film fusion bond epoxy pipeline occurred at a rock dent where the coating was damaged; the rock provided the shielding necessary for cracking. Shot peening is often confused with shot blasting, but these two processes have very different effects. Glass Cuts - The thing about glass cuts are that they are present in different variations from course to highly refined media but the work of both is excellent in giving the surface a new lustrous and reflective look. However, when this procedure is used for a dissimilar metal substrates such as aluminum, there is potential bimetallic corrosion. Contact| The choice of which grit to use depends on its intended purpose, the substrate, and the expense. Grit blasting is a technique that creating surface textures by the impact of hard particles.
Each has its own properties, which makes each one ideal for varying situations. Full coverage of the grit blast is indicated by lack of gloss on the metal surface when viewed at a flat grazing angle. Grit blasting is a relatively simple process. We believe that shot peening is the best option to treat critical parts used in industrial environments.
The sharpness of the abrasive and the consistency in size made it a great abrasive to use in giving uniform finished.
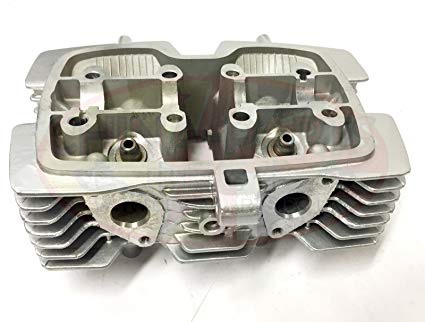
There are numerous types of grit. Grit blasting (or sand blasting) is a type of protective treatment that attempts to smooth out a part. They concluded that some improvements they observed in durability were strictly related to the increased surface area of the grit-blasted surfaces. Shot peening It is thus a plot of conductivity versus depth into the coating. Denser materials have more momentum and impart more energy to the substrate. It is often made into waterborne slurry and propelled by high-pressure water. The use of steel grit also has added advantages such as providing smoother surface finish and helping in peening which strengthens the metal. There are three main parts to any abrasive blasting tool regardless of what the specific material does to surface. Table 16.3. For reinforcement of a substrate or creating a very rough surface, a discontinuous layer of stainless steel such as 309 alloy may be applied to grit-blasted metal. Zinc conductivity as a function of depth over an aluminum substrate. This involves a blasting machine that comes equipped with a vacuum suction that removes any propelled abrasives and surface contaminants. Shot peening is a mechanical process that helps improve surface residual stresses for industrial metal parts. Everything You Need to Know About Powder Coating. Arc spray is most common. The rinse sometimes creates an oxidizing or rusting problem. Videos Waterjet cleaning The abrasive is soft, friable dried shells or nuts. Blasting with glass bead will produce a metallurgically clean surface for parts and equipment. Chemical etching using acidic materials, such as phosphoric acid, chromic acid, hydrochloric acid, or sulfuric acid or bases such as sodium hydroxide, gives smooth peaks, without the sharp tooth required for best adhesive bond. Its a unique form of abrasive blasting as the carbon dioxide is non-toxic and doesnt react with the contaminant on the part surface making it ideal for substances such as cleaning food processing equipment. Let's first clear up your mind about what is the Grit Blasting is and how does it function.
Solvent cleaning should always be carried out before this step. Whats universally true though is that its a much more effective way of cleaning surfaces and is more cost-efficient. Parts can also be pre-heated up to 200C to improve coating adhesion. Excessive noise and light radiation requires personal protective equipment. A drawback however to soda blasting is the abrasive cannot be recycled. Medical They found that increase particle size from 120150m to 380830m produced rougher surfaces. This process is used for cleaning or for preparing the surface for welding and also for adhesion of the coating. You must have heard about Grit blasting and its effects? Is Abrasive Blasting the Right Finish for You? This abrasive material is also fairly cheap to acquire and most abrasive blasting machines have been proven to be far more effective than other methods in terms of efficacy that is better and faster cleaning of surfaces. Significant differences in adhesion and conductivity can be seen. A profilometer drags a diamond stylus across the substrate and measures the depth of the peaks and valleys (Table 5.3). A finish machining process is usually required, e.g. As a result, this method is no longer preferred when it comes to abrasive blasting as the abrasive can be inhaled or leak into the environment. Coating bond strengths of up to 70 MPa can be achieved, although this is low in comparison to other coating processes. FAQs Porous surfaces can be sealed using wax (for low service temperatures), silicone and epoxy resins (for higher temperature/high humidity service environments). document.getElementById( "ak_js_1" ).setAttribute( "value", ( new Date() ).getTime() ); The periodic table is narrowing by the day, and scientists have fewer options for finding a compound with great coating qualities. Automotive Machine sanding has given slightly better results than hand sanding. Copyright 2022 Elsevier B.V. or its licensors or contributors. Glass-reinforced plastic laminates prepared for bonding by hand- and machine-sanding can be stored to 30 days at 23C and 50% RH with no adverse effect on bond strength.
Typical applications for baking soda include graffiti removal, boat hulls, and large printing press rolls. abrasive abrasives gravity specific hardness types which particle use blasting cleaning materials Hard grit is propelled by compressed air, or occasionally by high-pressure water, at the substrate needing cleaning or roughening. Some are even used against diamonds to alter their surfaces and in applications such as glass etching. Theres no abrasive that needs to be recycled or cleaned up. The biggest advantage and use for pencil blasting are when precision is needed. The abrasive used varies based on the surface treatment required. PRIMS Pro A photo of one example is shown in Figure8.8. This figure shows the conductivity of coatings as a function of the skin depth of the applied magnetic field. K.G. Glass beads are often used for stress relief. These results demonstrate the advantage of grit blast to the quality of the coating, and all coupon substrates used in the subsequent tests were grit blasted. They all have some mechanism to blast surfaces with an abrasive material that is, to propel abrasive at the surface at incredible velocities. This could be due to the relative softness of the substrate, or because the texture of the substrate or pattern machined in the substrate needs to be maintained. Figure 6.6.
With other clean substrates, the order of these two operations is not important.
Bristle blasting is the only blasting that doesnt involve an abrasive being projected onto a surface in order to clean it. blasting blast dry suction cabinets pressure cabinet guns nozzles gun diagram abrasive machine wet air glass hopper start need This makes them suitable for softer surfaces such as chrome, plastic, or glass. Many times it is necessary for sample processing to take place to lock in the final media type and size. Plastic grit, walnut shells, or sodium bicarbonate can clean the substrate or remove the previous coating. Powder coating is a type of dry coating often used as a finish on industrial equipment as well as home goods. Baking soda is commonly used where one-pass coverage with no recovery is acceptable or desirable, and the substrate is delicate or sensitive. Search| In addition, the etching reagents require immediate rinse to stop the action and prevent salts from depositing on the surface. If you are looking for a process to clean out any surfaces of your belongings then you are in the right place. [67] found that grit blasting can enhance bonding between polyamide and AA6082 while a higher pressure did lead to a higher bonding strength (Fig. But even when chemically analyzed virgin grit material is used, tests have shown that the method yields bonds to steel adherends exhibiting poor durability. Contact us today to inquire about utilizing our shot peening service. Silicon carbide is usually offered in a size range of 16240 grit. Grit blasting, also known as Sandblasting is a mechanical process of removing dust, rust, and impurities from the surface of any material. It uses silica or quartz as the abrasive material, which is then propelled onto surfaces at high speed. of Shot Blasting Machine, Shot Blasting Machine for Surface The different media types have different hardness, shape, and density, and each is available in a wide range of particle sizes. One surprising result of the laboratory and field studies was that a light brush blasted surface was actually more susceptible to SCC than a mill scaled, wire brushed surface and that a near white surface finish was required for adequate SCC resistance [6,7].

